FWM Lok 4 Arbeitsberichte
Aus GILLBACHBAHN
Admin (Diskussion | Beiträge) (→Duis ac sem tortor) |
Admin (Diskussion | Beiträge) (→Lorem ipsum dolor sit amet) |
||
Zeile 2: | Zeile 2: | ||
Vor zwei Wochen weilte zu einer Arbeitswoche beim FWM Oekoven, wo die Dampflok Nr.4 (Jung 9294/1941 Typ Hilax, 65PS) seit mehreren Jahren eine Hauptinstandsetzung erhält. | Vor zwei Wochen weilte zu einer Arbeitswoche beim FWM Oekoven, wo die Dampflok Nr.4 (Jung 9294/1941 Typ Hilax, 65PS) seit mehreren Jahren eine Hauptinstandsetzung erhält. | ||
Das Fahrwerk befand sich noch im zerlegten, jedoch aufgearbeiteten Zustand. Die Radsätze waren bereits vor längerer Zeit neu profiliert und damit von den Flachstellen der Spielplatzzeit befreit worden. | Das Fahrwerk befand sich noch im zerlegten, jedoch aufgearbeiteten Zustand. Die Radsätze waren bereits vor längerer Zeit neu profiliert und damit von den Flachstellen der Spielplatzzeit befreit worden. | ||
- | Im Rahmen dieser Instandsetzung sollten einige Veränderungen vorgenommen werden. So wurden die bislang rot lackierten Stangen wieder blank gemacht. | + | Im Rahmen dieser Instandsetzung sollten einige Veränderungen vorgenommen werden |
+ | |||
+ | [[Datei:FWM-Lok4-HU00002.jpg|400px|thumb|right|So wurden die bislang rot lackierten Stangen wieder blank gemacht. suscipit ligula vitae elit pharetra, eget interdum libero fermentum. Fusce faucibus, nibh eu vehicula dapibus, sapien diam auctor tortor, ut viverra leo erat et purus. Duis sollicitudin libero id turpis pulvinar, a auctor mi lacinia. Praesent auctor est et nulla posuere auctor. Fusce varius enim a erat consequat faucibus. Morbi elit felis, cursus ac laoreet nec, sollicitudin dignissim justo. Duis vitae adipiscing sapien. Duis purus nibh, consequat vel ante sit amet, ultricies auctor tellus. | ||
+ | ]] | ||
+ | |||
+ | |||
Die bei der ersten Restaurierung vor rund 20 Jahren neugebauten Kohlekästen und Führerhausteile waren bislang mit Nietkopfschrauben zusammengefügt. Um den historisch gerechten Zustand wiederherzustellen wurden diese nun entfernt und die Bauteile wieder genietet. | Die bei der ersten Restaurierung vor rund 20 Jahren neugebauten Kohlekästen und Führerhausteile waren bislang mit Nietkopfschrauben zusammengefügt. Um den historisch gerechten Zustand wiederherzustellen wurden diese nun entfernt und die Bauteile wieder genietet. | ||
Die Nietlöche wurden auf der Außenseite angesenkt, da dort ein Senkkopf geformt wird. | Die Nietlöche wurden auf der Außenseite angesenkt, da dort ein Senkkopf geformt wird. |
Version vom 22:50, 3. Mai 2014
Inhaltsverzeichnis |
Lorem ipsum dolor sit amet
Vor zwei Wochen weilte zu einer Arbeitswoche beim FWM Oekoven, wo die Dampflok Nr.4 (Jung 9294/1941 Typ Hilax, 65PS) seit mehreren Jahren eine Hauptinstandsetzung erhält. Das Fahrwerk befand sich noch im zerlegten, jedoch aufgearbeiteten Zustand. Die Radsätze waren bereits vor längerer Zeit neu profiliert und damit von den Flachstellen der Spielplatzzeit befreit worden. Im Rahmen dieser Instandsetzung sollten einige Veränderungen vorgenommen werden
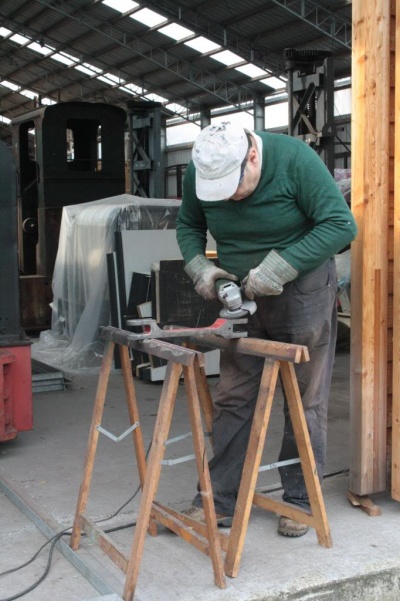
Die bei der ersten Restaurierung vor rund 20 Jahren neugebauten Kohlekästen und Führerhausteile waren bislang mit Nietkopfschrauben zusammengefügt. Um den historisch gerechten Zustand wiederherzustellen wurden diese nun entfernt und die Bauteile wieder genietet.
Die Nietlöche wurden auf der Außenseite angesenkt, da dort ein Senkkopf geformt wird.
Mit Hilfe verschiedenster eigens angefertigter Gegenhalter wurden die Einzelteile des linken Kohlekastens zusammengenietet. Dabei war zunächst eine Reihenfolge für den Zusammebau festzulegen, damit am Ende auch alle Niete zugänglich sind. Hier im Bild die Außenwand.
Geschlagen wurden die Niete warm und sämtlich von Hand.
Sind alle Einzelbleche mit ihren zugehörigen Winkeln vernietet, geht es an den Zusammenbau. Hier müssen die letzten Nietreihen von Innen gegengehalten werden, was bei einer lichten Weite von 355 mm alles andere als bequem ist.
Der linke Kohlekasten ist nach zwei Tagen und rund 200 geschlagenen Nieten fertig.
Die Einzelteile für den rechten Kohlekasten liegen bereit.
Hier ist durch den integrierten Werkzeugkasten im oberen Bereich noch weniger Platz im Inneren.
Und wieder wird genietet. Zunächst wird nur jeder zweite Niet geschlagen, dazwischen sichern Heftschrauben die paßgenaue Lage der zu verbindenden Teile zueinander.
Der rechte Kohlenkasten nimmt Gestalt an.
In der Zwischenzeit wurde auch ein neuer Aschkasten für die Lok gebaut.
Vorbereitung für das Einachsen.
Das eingeachste Fahrwerk auf der Hubbockanlage. Nun konnte bequem die Bremsanlage montiert werden.
Vor der Montage der Kuppelstangen wurden Lehrdorne mit dem jeweiligen Zapfendurchmesser gedreht, um das Stichmaß der Stangen kontrollieren zu können.
Ein Stangenlager musste anschließend um 5/10 mm korrigiert werden.
Nach dem Anbau der Stangen konnte die das Fahrwerk mit vereinten Kräften aus der Halle geschafft werden.
Die Schlosserbrigade vor dem auf der Schiebebühne befindlichen Fahrwerk.
Auf der Arbeitsgrube wurden am Abend noch die Achsstellkeile, Stangenlager und die Bremse gestellt.
Am nächsten Tag ging es mit dem Nieten des Führerhausoberteils weiter. Hier waren besonders lange Gegenhalter notwendig.
Inzwischen war der Aschkasten fertig geschweißt und grundiert.
Anprobe am Rahmen. Passt!
Nach dem Anbau des Aschkastens an den Bodenring erfolgte das Aufsetzen des Kessels auf den Rahmen.
Das erste Mal seit langer Zeit sind beide Hauptbaugruppen wieder vereint.
Auf der Arbeitsgrube wurden dann noch die Bedienhebel für Aschkasten- und Luftklappe montiert.
Eine abschließende Probefahrt gezogen von einer Diesellok zeigte eine wesentliche Verbesserung der Laufeigenschaften gegenüber dem Zustand vor der HU.
Innerhalb dieser Woche wurde ein großer Schritt in Richtung Wiederinbetriebnahme geschafft, dank der tollen Mannschaft und der guten Verpflegung!
Für mich waren insbesondere die Nietarbeiten eine lehrreiche Erfahrung, in solch großem Umfang mit rund 500 geschlagenen Nieten habe ich das auch noch nicht gemacht.
Die dabei gewonnen Erkenntnisse werden auch bei anderen Projekten noch sehr hilfreich sein.
Nochmals herzlichen Dank an tolle Truppe vom FWM!
suscipit ligula vitae elit pharetra, eget interdum libero fermentum. Fusce faucibus, nibh eu vehicula dapibus, sapien diam auctor tortor, ut viverra leo erat et purus. Duis sollicitudin libero id turpis pulvinar, a auctor mi lacinia. Praesent auctor est et nulla posuere auctor. Fusce varius enim a erat consequat faucibus. Morbi elit felis, cursus ac laoreet nec, sollicitudin dignissim justo. Duis vitae adipiscing sapien. Duis purus nibh, consequat vel ante sit amet, ultricies auctor tellus.
Lorem ipsum dolor sit amet
consectetur adipiscing elit. Integer hendrerit dui at condimentum pulvinar. In elementum tempus libero ornare molestie. Nam consectetur aliquam feugiat. Donec suscipit ligula vitae elit pharetra, eget interdum libero fermentum. Fusce faucibus, nibh eu vehicula dapibus, sapien diam auctor tortor, ut viverra leo erat et purus. Duis sollicitudin libero id turpis pulvinar, a auctor mi lacinia. Praesent auctor est et nulla posuere auctor. Fusce varius enim a erat consequat faucibus. Morbi elit felis, cursus ac laoreet nec, sollicitudin dignissim justo. Duis vitae adipiscing sapien. Duis purus nibh, consequat vel ante sit amet, ultricies auctor tellus.
Lorem ipsum dolor sit amet
consectetur adipiscing elit. Integer hendrerit dui at condimentum pulvinar. In elementum tempus libero ornare molestie. Nam consectetur aliquam feugiat. Donec suscipit ligula vitae elit pharetra, eget interdum libero fermentum. Fusce faucibus, nibh eu vehicula dapibus, sapien diam auctor tortor, ut viverra leo erat et purus. Duis sollicitudin libero id turpis pulvinar, a auctor mi lacinia. Praesent auctor est et nulla posuere auctor. Fusce varius enim a erat consequat faucibus. Morbi elit felis, cursus ac laoreet nec, sollicitudin dignissim justo. Duis vitae adipiscing sapien. Duis purus nibh, consequat vel ante sit amet, ultricies auctor tellus.
Duis ac sem tortor
In der vergangenen Woche wurden die Arbeiten an der Lok weitergeführt. In den Wintermonaten wurden zahlreiche Teile überarbeitet oder neu gefertigt. Hauptschwerpunkt der Arbeitswoche war die äußere Steuerung. Da die Lok in der Vergangenheit ausgesprochen schlechte Laufeigenschaften aufzeigte, ist eine Grundberichtigung der Steuerung notwendig. Diese wurde mit der Bearbeitung der Kreuzkopfgleitbahnen begonnen. Anhand der ungleichmäßigen Verschleißspuren an den Anfang der 90er Jahre neu angefertigten Teile war klar, dass auch diese Grundberichtig werden mussten. Zunächst wurden diese vermessen und anschließend auf die erste Ausbesserungsstufe abgeschliffen. Eine Gleitbahn war durch falsche Montage verzogen und musste gerichtet werden, bevor sie auf die Schleifmaschine aufgespannt werden konnte. Um nun bei der neuerlichen Montage eine korrekte Ausrichtung durchführen zu können wurde eigens eine Zentriervorrichtung angefertigt, mit der die Zylinderachse ermittelt und dargestellt werden kann. Diese dient bei der Berichtigung der Gleitbahnlage als Referenzachse. Durch die Zentriervorrichtung wird ein Spezialdraht gezogen und über den Treibzapfen mit Gewichten abgespannt. Durch Verfahren der Lok wird er konzentrisch auf die Zylinderachse ausgerichtet und fixiert. Anschließend konnte die Gleitbahn provisorisch montiert und in ihrer alten Lage ausgerichtet werden. Dabei zeigte sich, dass das Stichmaß zwischen der Stiftschraube am Zylinderdeckel und dem Gleitbahnträger um 2,2 mm von dem auf der linken Gleitbahn abwich. Um die Gleitbahn dennoch montieren zu können, hatte man offensichtlich den Zentrieransatz der Sechskantmutter am Zylinderdeckel abgedeht. Eine korrekte Ausrichtung war damit unmöglich und ursächlich für die zuvor behobenen Schäden. Hier war eine Stichmaßkorrektur durch das Anfertigen eine Beilage unter dem Gleitbahnträger notwendig. Auch die Lageabweichungen zur Zylinderachse wurden messtechnisch ermittelt und müssen nun durch die Anfertigung entsprechender Beilagen behoben werden. Leider musste dies, aufgrund der einfachen Werkstattausstattung vor Ort, außerhalb erfolgen und war zum Ende der Woche noch nicht abgeschlossen. Um nicht zu viel Zeit zu verlieren wurde sich nun des Steuerbocks angenommen, der ebenfalls unzulässig große Spiele und Verschleißerscheinungen aufwies. Die Bohrung für den Fußlagerzapfen wurde ausgebohrt und ausgebuchst, die beiden Schrauben an der Handfalle des Steuerhändels ausgebaut und gegen neu gedrehte Bolzen ausgetauscht, nachdem die Bohrungen aufgerieben worden sind. Die Handfalle wurde gerichtet, mit Paßschreiben versehen und poliert. Der Handgriff des Steuerhändels war bei der letzten Restaurierung als Drehteil neu entstanden und lediglich an den Schaft angeschraubt worden. Diese Verbindung hatte sich als nicht sonderlich haltbar erwiesen. Nach dem Polieren des Griffstücks wurde es daher sauber mit dem Schaft verschweißt und verschliffen. Am nächsten Tag erfolgte die Montage des Steuerbocks an den bereits teillackierten rechten Kohlekasten. Bei der Montage fiel auf, dass die Distanzstücken zwischen de Zahnbögen von Haus aus zu stark angefertigt waren. Es war daher notwendig sie für die Verrichtung des erheblichen Seitenspiels zu schwächen. In Ermangelung eine Fräsmaschine geschah dies auf der kleinen Waagerechtstoßmaschine in der Oekovener Werkstatt, die für die notwendige Genauigkeit gerade noch ausreichend gewesen ist. Anschließend wurde der Zahnbogen wieder montiert. Das Fußlager des Steuerhändels musste ebenfalls berichtigt werden, da der Zapfen nicht konzentrisch mit dem Zahnbogen war und die Handfalle bei vorwärts ausgelegtem Steuerhändel mit den Zähnen kollidierte. Es erfolgte nun die Montage der Stehkesselverkleidung, die nach Anbau der Kohlekästen nicht mehr vollständig zugänglich sein wird. Da die auswärts zu fertigenden Dreh- und Frästeile noch immer auf sich warten ließen wurde nun der Einbau der Schieber in Angriff genommen. Die Schieberstangen waren in den vergangenen Monaten vermessen, gerichtet und geschliffen worden. Die Stopfbuchsen und Schieberführungsbuchsen waren ebenfalls erneuert worden. Letztere mussten jedoch noch vor Ort eingepasst werden. Sie wurden dafür zunächst von einem Vereinsmitglied in eigener Werkstatt ausgedreht und später von mir noch am Außendurchmesser abgedreht. Um sie vernünftig spannen zu können, habe ich sie weich zusammengelötet. Das Abdrehen erfolgte dann in der FWM-Werkstatt. Nach dem Abschaben der Lotreste konnten die Führungsbuchsen in die Schieberführungen eingepasst werden. Leider war auch an den Stopfbuchsen etwas Nacharbeit notwendig. Einbau der rechten Schieberstange. Die Stopfbuchsgrundringe müssen noch erneuert werden. Erst nachdem beide Schieberstangen montiert waren, fiel mir unter mehreren dicken Farbschichten an der rechten Schieberführung die eingeschlagene Markierung L 9294 auf. Da die Führungen im Rahmen dieser Hauptinstandsetzung bisher nicht abgebaut wurden, handelte es sich um einen früheren Montagefehler. Solche Teile werden im Allgemeinen in einer Aufspannung mit der Bohrung im Zylinder bearbeitet, um Abweichungen in der Lage der Bohrungen zu vermeiden. Daher war es notwendig die Teile wieder an ihre richtigen Seiten zu tauschen. Da die Schieberstangen selbst richtig zugeordnet waren, mussten auch die Führungsbuchsen nochmals getauscht werden. Nach einer weiteren Stunde Arbeit waren nun alle Teile an der richtigen Stelle. Im Vergleich zur ersten Arbeitswoche war das Ergebnis wegen der vielen Anpassungsarbeiten und Fremdleistungen etwas überschaubarer, jedoch bedarf eine Grundberichtigung eben viel Sorgfalt und Zeit. Wenn die Maschine am Ende ihre eigentliche Leistungsfähigkeit zurückerlangt hat, werden sich diese Mühen gelohnt haben.
Maecenas ac erat mauris. Proin ut orci nec est adipiscing mollis adipiscing et arcu. Etiam lacinia pretium odio id vulputate. Cras eu volutpat elit. Curabitur cursus eleifend massa eu blandit. Proin ac eros consequat, pulvinar urna eget, tincidunt ligula. Duis non odio at mi placerat porttitor. Duis porttitor nulla purus, non consectetur diam suscipit et. Cras id tellus lobortis, rutrum enim et, varius dolor. Cras sit amet neque non ante porta egestas quis non mauris. Nam mollis massa vel purus pulvinar rutrum. Praesent tempus in mauris vel semper. Pellentesque id orci mi.
Aenean euismod convallis massa, sit amet egestas enim sagittis quis. In sem sem, fringilla at sapien in, egestas blandit massa. Maecenas suscipit posuere massa, nec commodo mauris sodales a. Etiam vitae tortor rhoncus, posuere augue sed, cursus erat. Duis lobortis aliquam lectus, in ultricies odio lacinia et. Sed sagittis, augue non gravida molestie, odio erat laoreet sapien, ultrices tincidunt nisi odio at elit. Sed vel luctus libero, id volutpat elit. Praesent scelerisque nisl quis dolor congue consequat.
Nam et turpis eleifend, dignissim velit non, tincidunt sapien. Vestibulum vitae fringilla diam. Sed placerat, nulla eu sollicitudin tempus, turpis magna commodo tortor, quis sagittis neque tellus lacinia nisl. Maecenas nec venenatis lectus, quis faucibus erat. Nulla nec risus adipiscing, convallis urna pulvinar, iaculis sapien. Vivamus venenatis diam non leo pretium vulputate. Integer vel feugiat nisl.